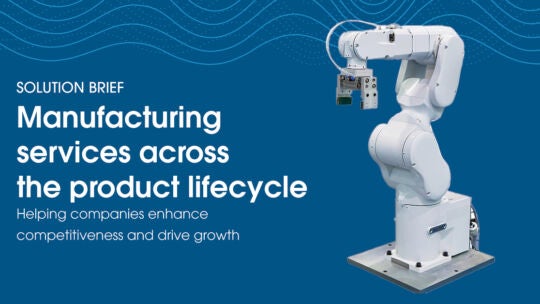
We’ve integrated these smart technologies into our factories around the world to increase quality and efficiency.
On our factory floors, we’ve automated repetitive tasks, as well as tasks that are difficult for humans due to physical constraints. The use of robotics in tight spots, for example, has become increasingly popular as the market for miniaturized electronics has grown. While some robots perform independent tasks, many robots, known as cobots, collaborate with humans to complete their work.
We’re fully invested in full stack smart automation processes, which allow us to migrate and automate most of the operations work needed for applications, middleware, hardware, and data-center infrastructure. This means we can quickly provide you with a customized, automated manufacturing line.
In addition, artificial intelligence and advanced analytics alert us before machines need maintenance, which reduces downtime and increases throughput on our factory lines. And it’s all based on leading advanced manufacturing technologies and capabilities.
When it comes to speeding your time-to-market, lowering risk, and improving efficiencies, insights are everything. That’s where digital manufacturing comes in.
From sensors to internet-of-things (IoT) platforms like iENBL, and data management solutions that incorporate advanced analytics, machine learning, and failure analysis, our capabilities and expertise span the entire digital manufacturing ecosystem. We’re continuously gathering data using connected cells that stack up to a closed-loop system for improved manufacturing performance.
Our deep knowledge of sensors, connectivity solutions, and cloud and edge computing give you the visibility and agility of smart automation. We work to monitor machine health, identify process improvements, and increase safety so you can reduce downtime and fuel data-driven decision making for your business.
Get a complete picture of smart, digital factory operations through 13 industrial sensors that measure vibration, humidity, temperature, and pressure, as well as video, optics, and much more.
With dedicated research efforts that define rulesets for new automation developments, we’re constantly exploring new ways of sensing and improving automation. We can also process, enrich, connect, compute, and store data through gateways and extract transform load (ETL) processes. Through all of this, we deliver the benefits of extensive connectivity knowledge, access to cloud technologies, and artificial intelligence and machine learning capabilities.
When building new products, or introducing changes to existing products, companies can speed time-to-market and identify potential issues by using simulation to visualize production processes and product lifecycles. We’ve integrated our simulation expertise across every facet of our organization to drive throughput, optimize processes, and increase efficiency.
We’ve incorporated advanced simulation and modeling techniques across our factories, accelerating time-to-market, improving yields, and reducing cost and waste. Through an integrated approach to digitally testing production lines, products, and more, we can make sure the right designs, equipment, and processes are in place without affecting time, resources, or capital in the real world.
We can help you visualize the steps taken in your product lifecycle, including how it’s made, how it works, and where it can be improved. We then take those results and optimize your entire process using discrete event simulation practices.
No matter what stage your product is in, our team can simulate the best path forward. We can help you imagine how the assembly line will work — in any situation. Whether you’re setting up a line for the first time, optimizing an existing line, preparing for an increase in demand, or transitioning a line to your next-generation product, we can simulate the best decisions, every time.
With years of simulation experience, we’ve created best practices, not only in advanced simulation, but also in standard procedures and practices for every step along the way. From requesting to reporting, our advanced simulation capabilities allow our customers to relax. We put the effort into building the models — our customers benefit from the insightful, outcome-based results.
Our strategic investments have allowed us to use and implement advanced simulation and statistical software that enable highly complex simulations. Our team is focused on designing and formulating powerful mathematical models and algorithms to solve the most complicated problems in manufacturing environments — and then using those models to set up highly efficient processes.
Our real-time advanced simulation capabilities speed product startup, improve yields, and reduce ramp costs via digital twins of factory operations.
Additive manufacturing, such as 3D printing, optimizes your designs for better functionality, product customization, and parts and cost management. With the ability to make parts on demand, you can reduce lead times and minimize excess inventory.
It’s easy to get started. We offer technical and application support at any stage of the product lifecycle. This includes feasibility studies to qualify technologies and determine what’s best for you.
In each region, we provide a full suite of in-house industrial additive manufacturing technologies, including state-of-the-art software, hardware, and materials. We can help you visualize your products with concept models, create rapid prototypes to shorten product development cycles, and make end-use parts to simplify your supply chain. In addition, our 3D printing solutions go beyond traditional subtractive processes and can render highly intricate geometries.
By using additive manufacturing, we can help integrate your designs more quickly, reduce development time, and shorten lead times for components — all in support of your high-mix, low-volume production needs.
By eliminating waste in our processes, we’re always moving faster according to Lean principles. But we also make sure faster does not mean rushed by using Six Sigma to drive data-driven decision making and process improvement toward a reduction in variation.
Plus, our learnings are yours — we make sure the knowledge transfers through customer workshops that build more trustworthy partnerships.
For us, quality manufacturing isn’t just a vision. Measuring is believing, so we benchmark progress monthly using our Continuous Improvement Maturity Tracker, which measures Lean Six Sigma engagement in our organization across 19 elements in seven categories.
Additionally, our efforts to continuously optimize our manufacturing models enjoy robust support from our Global Business Excellence (GBE) and Quality organizations. GBE supports approximately 100 sites worldwide, applying our Lean Six Sigma Agile methodology across all the industries we serve.
These are the goals driven by our Kaizen to Business Needs workshops. We’ve set quality targets for productivity improvement, inventory reduction, lead time reduction, scrap elimination, and defects elimination.
And because people are our most valuable assets, we regularly hold internal Kaizen workshops to equip our teams with the resources and tools they need to reach those targets — and then set even higher ones.
Staying Lean means amplifying value-added activities so manufacturing operations can move faster and produce less waste. For example, why automate what’s not useful? Using proven Lean tools, we identify and reduce the number of non-value-added activities so you can maximize the value and effectiveness of advanced manufacturing technologies.
Through best practice sharing, industry benchmarking, and a global Lean Six Sigma competition with more than 300 participating teams, we make sure we are advancing the latest in efficiency and mistake proofing.
We deploy systematic process improvements at our ISO-certified manufacturing facilities using Define, Measure, Analyze, Improve, and Control (DMAIC) and Design for Six Sigma (DFSS) methodologies to reduce variation, eliminate scrap and rework, and implement process control.
For regulated industries like healthcare and automotive, you can have confidence in our fully compliant product creation and scaling capabilities. We have also made impressive progress on our Quality 4.0 implementation, putting us on par with fewer than 30 percent of companies worldwide that have taken this leap. Our Quality 4.0 program is built on a strong foundation of our quality management system across multiple standards.
We leave no stone unturned in our continuous improvement journey. That means suppliers and customers are vital contributors in our end-to-end process. We’re constantly engaging all parties to deliver the highest quality products and reduce manufacturing cost through improved efficiency.
We start by choosing the right partners through our Preferred Supplier Program, which helps us select suppliers that meet or exceed our quality and cost standards (among other factors).
And ask any Flex employee — internal team involvement spans all levels of our culture of continuous improvement.