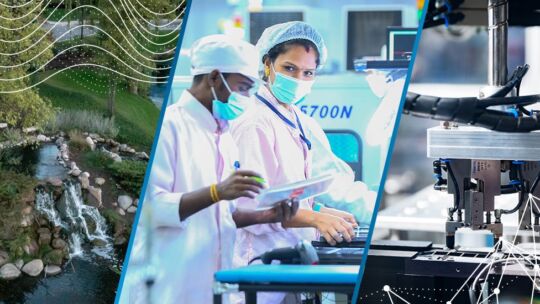
A better future starts with measurement and science, which is the basis of our sustainable manufacturing practices and targets for reducing emissions, water usage, and achieving zero waste. We also engage with local NGOs and an employee volunteer program to improve the quality of life in our communities.
It’s our people who create the extraordinary, every day. We strive to ensure team members are empowered to reach their full potential by promoting a culture of safety, inclusion, and continuous development. We also invest in mental health resources and hold our facilities to the highest global standards for labor practices.
What defines our approach? We do the right thing, always. Whether we’re helping customers deliver great products, addressing sustainability requirements with suppliers, or collaborating with customers and suppliers to further a more sustainable value chain, responsibility and transparency inform our every action.
Our advancement of sustainability includes clear, consistent communications about our goals, activities, performance, and results.
Environment
27% reduction in absolute scope 1 and 2 greenhouse emissions in 2022 from 2019 baseline year
Health and Safety
17% reduction in total case incident rate (TCIR) in 2022
Suppliers
35% of preferred suppliers had greenhouse gas emissions reduction targets in 2022
reduction in absolute scope 1 and 2 greenhouse emissions in 2022 from 2019 baseline year1
waste diverted from landfill globally in 2022
of our sites with 1,000 employees or more partnered with a local NGO in 2022
1 The target boundary includes biogenic emissions and removals from bioenergy feedstocks. Absolute Scope 1 and 2 market-based emissions.
Our journey to reduce our environmental footprint and ambition to reach net zero emissions by 2040 focuses on implementing and purchasing renewable energy, optimizing site infrastructure, and partnering with our ecosystem of customers and suppliers on energy and emissions reduction strategies.
Meanwhile, we’re charting a path to zero waste by applying our circular economy practices to reuse, repurpose, and extend the use of materials. In addition to our commitment to decreased water consumption, we participate in the World Business Council for Sustainable Development’s WASH Pledge to increase safe water access at all our workplaces.
2 The target boundary includes biogenic emissions and removals from bioenergy feedstocks
3 Per revenue
We don’t just want to just protect the planet — we aspire to uplift and invest in the communities where we operate and empower our employees to do so too. Our community building investment approach is two-fold: strategic initiatives supported by the Flex Foundation and employee involvement globally.
Our community building efforts are aligned with four strategic UN Sustainable Development Goals: #3 good health and wellbeing, #8 decent work economic growth, #12 responsible consumption and production, and #13 climate action.
4 Sites with more than 1,000 employees
Our 2023 annual sustainability report is a summary of our most important sustainability activities, performance, and results from the 2022 calendar year.
decrease in safety incident rate year over year in 2022
of our employees had access to emotional / mental health programs in 2022
average hours of training
per employee achieved in 2022
We promote workforce safety, health, and well-being from all angles. Our strong social management system aligns to the RBA code of conduct as we pursue industry certifications to ensure the respectful treatment of workers and the consistent adherence of responsible business practices.
By investing in Industry 4.0 technologies and staying apprised of equipment safety improvements, we’re continuously designing risk out of manufacturing processes.
The diversity of our teams serves as a competitive advantage and spans background, experience, talent, education, gender identity, race, ethnicity, and ability.
Together, we’re working toward more equitable outcomes that strengthen gender, racial, and ethnic diverse representation through employee empowerment, enhanced opportunities, and resource accessibility. And we do it all through a culture of inclusion rooted in mutual respect.
We promote and protect human rights to safeguard the fundamental freedoms of our workforce and treat team members with the utmost respect, dignity, and care. This includes providing well-being and development resources.
We recognize the importance of accessible mental health programs to support team members, psychologically and emotionally. We’re continuing to evolve and develop formal and on-the-job learning and upskilling opportunities so that every team member is empowered to prepare for their next role while gaining valuable experience.
Our 2023 annual sustainability report is a summary of our most important sustainability activities, performance, and results from the 2022 calendar year.
of preferred suppliers had
greenhouse gas emissions
reduction targets in 2022
of specified customers1 had science-based targets in 2022
Recognized as one of the
World’s Most Ethical
companies by Ethisphere
for our leading in ethical
business practices in 2023
1 Flex committed that 70% of customers as measured by emissions covering purchased goods and services, capital goods, and use of sold products will have science-based targets by 2025.
We hold our supplier network to the highest ethical standards by requiring strong management systems, transparent reporting, effective social and environmental activities, ethical practices, and comprehensive risk mitigation. We also work to reduce emissions across the value chain by working with suppliers to set reduction targets by sharing lessons learned and scaling best practices.
We’re helping leading brands identify the optimal route to reduce emissions, waste, and energy while balancing lead time, cost, and sustainability requirements through our circular economy solutions. We also partner with a set of our customers to help them identify science-based emission targets, accelerating a more sustainable value chain.
Integrity starts at the top and serves as the foundation of trust for our employees, customers, and other stakeholders. In everything we do, we maintain the highest standards of ethical business practices and compliance with integrated scorecards for risk assessment, code of business conduct and ethics training for direct and indirect labor, and more. In addition to local reporting channels, we have a toll-free hotline and online reporting channel available 24 hours, 7 days a week in several languages.
We never stop evaluating and enhancing our oversight processes and procedures to ensure the highest levels of accountability and transparency, as reflected in our strong ratings in the Dow Jones Sustainability Index (DJSI), Morgan Stanley Capital International (MSCI), and Institutional Shareholder Services (ISS). We also maintain strong oversight through annual review of committee composition.
Our 2023 annual sustainability report is a summary of our most important sustainability activities, performance, and results from the 2022 calendar year.