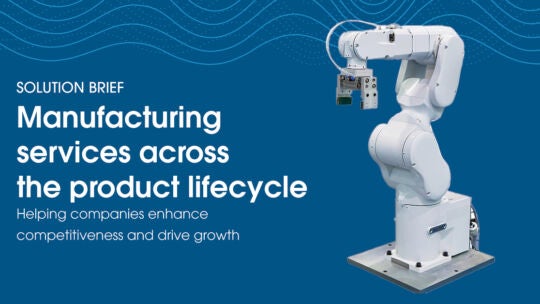
A lot goes into successfully bringing high-quality, reliable products to market — but what are some of the tools that enable that success?
One particularly powerful example is simulation and modeling tools. Simulation is the process of modeling a real phenomenon through a set of mathematical formulas or algorithms. Simulation and modeling tools allow you to virtually model a process in detail without having to spend the time, resources, or capital to physically test that design in a real-world environment.
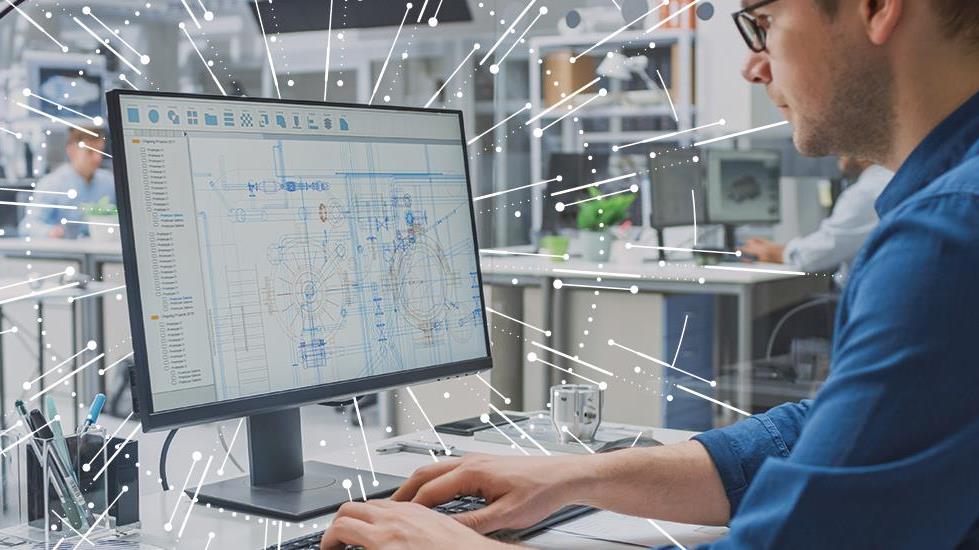
Three types of simulation that accelerate time-to-market and reduce cost and waste
1. Discrete-event simulation
Discrete-event simulation (DES) allows you to model and analyze highly complex systems and processes to help make business decisions and drive improvements. DES is a particularly powerful simulation tool because it uses a real-world environment modeled into a software-created environment, creating a digital twin. With this digital twin, DES allows you to test ‘what-if’ scenarios as well as evaluate various other systems analysis techniques.
DES can be used in the planning process long before a real system is installed, providing insights to make fast, reliable decisions in the early stages of production planning. Those insights can then be used across the product lifecycle to simulate environments such as production lines, automation solutions, logistic operations, or other manufacturing processes.
With DES, you can:
- Improve productivity
- Optimize volumes
- Optimize layouts
- Reduce lead time
- Reduce work in progress
2. Design for Reliability
Before your product comes to life, Design for Reliability (DfR) testing identifies high-risk areas and suggests tests for validating results. The primary goal of DfR is to prolong high-level performance of a product. While mainly used in the design stage, DfR can be used at any stage in a product’s lifecycle.
DfR can help you:
- Meet your reliability target
- Optimize product design
- Reduce costs
3. Finite element analysis
Conducting finite element analysis (FEA) ensures a product can handle various types of stress. FEA is used to optimize the design of a part to improve the design, avoid possible failures, and validate the existing geometry for its application. FEA is commonly used in the design stage of a product before the parts are fabricated, but can benefit existing products for design validation purposes.
With FEA, you can:
- Improve product reliability
- Reduce the steps of physical testing
- Simulate ‘what if’ scenarios
Want to find out how our simulation expertise can help you optimize your products?