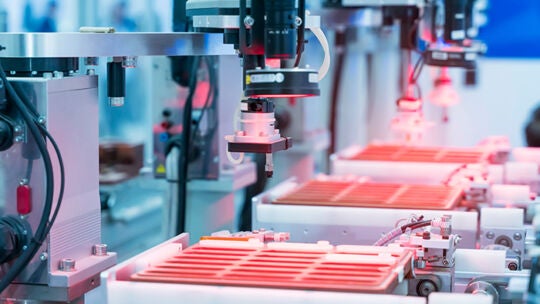
Today, the healthcare industry faces unprecedented challenges due to rising cost pressures across all areas of care. In an industry in which bringing a new medical device to market can take three to seven years or more, and an average of 12 years for new drug approvals, it is critical to be able to move faster and more efficiently while still upholding standards of reliability and quality.
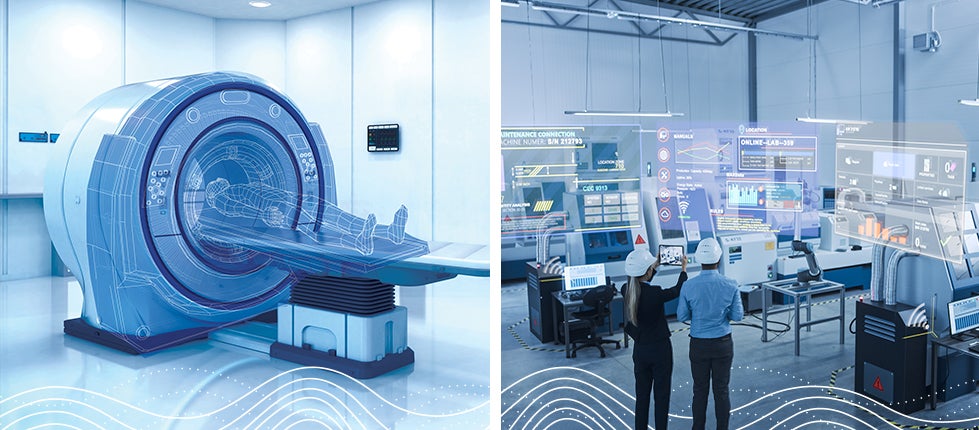
One avenue to continually seek ways to reduce risk and reinvest resources into product innovation is by outsourcing to trusted partners. Outsourcing in the healthcare industry is not just a strategy; it’s a game changer. Outsourcing can support a broad spectrum of strategies, from leveraging external manufacturing partners to enhancing operational efficiency, to driving significant business transformation—often referred to as “network optimization.”